- What we do?
Die Maintenance
Maximize Die performance with our precision maintenance service for seamless manufacturing.
- Uncover Benefits
Advantages of Die Maintenance
Our expert maintenance services ensure stable operation and prolonged die lifespan for die rollers and associated accessories, promoting sustained functionality.
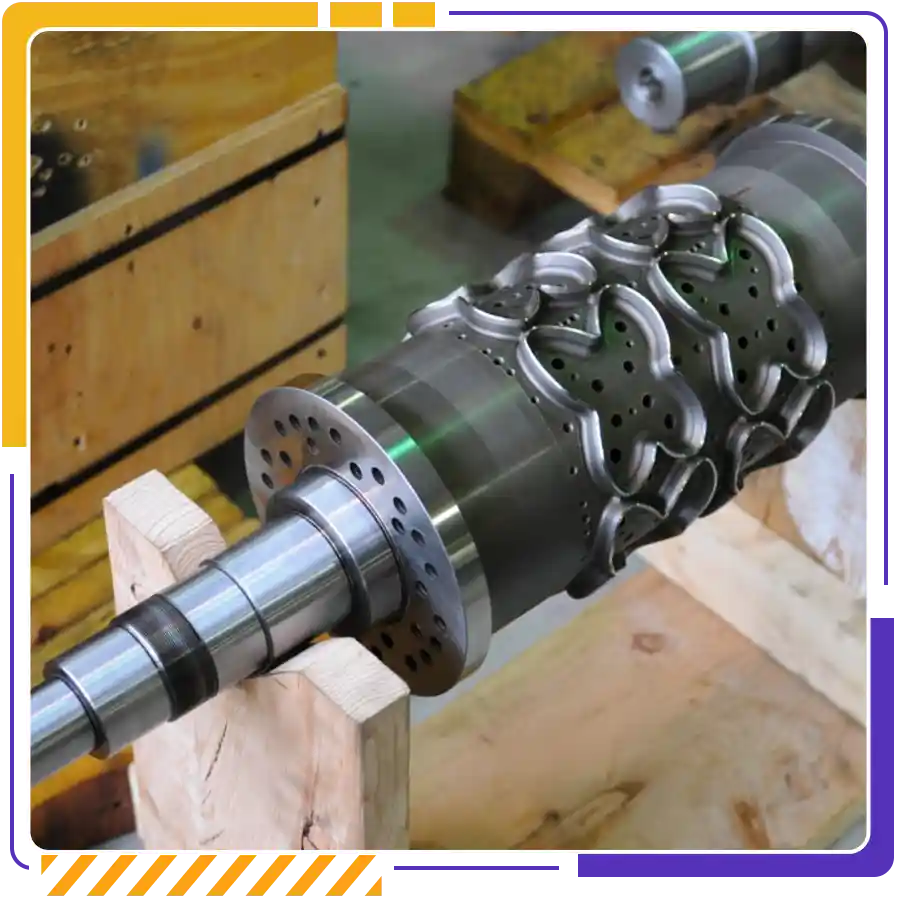
- Extends the life of your dies
- Ensures proper functionality
- Meets OEM Specifications
- Lower risk of breakdowns
- Increase efficiency
- Decrease unplanned downtime
- Promote health and safety
- Die Revitalization
Process involved in
Die Maintenance Service
Die Inspection
Inspection of dies is a crucial step in the manufacturing process to ensure their quality and functionality. Dies are used in various industries, including metal stamping, plastic moulding, and semiconductor manufacturing.
Ensuring customer satisfaction, reducing defects and maintaining product integrity are its key roles.
Initially, We engages in examining, testing, and measuring the physical and operational characteristics of a die.
This process may include visual inspection, dimensional inspection, functional inspection, or performance inspection, depending on the die and its specifications.
- Identify and record issues
-
Review the issues
(e.g. Damages, Dimensions, Run out, etc.) - Examine the effectiveness of your Die and Compare with past service History.
- Check for compliance with customer and do the needful to resolve it.
- Recommend corrective actions to rectify or eliminate the issues.
Re Grinding
Experience precision at its finest with our die grinding services, featuring advanced CNC and hydraulic grinding machines for die-cut rollers and flatbed dies.
We ensure optimal results when operating with a range of up to 350mm in diameter and 1500mm in roller length.
Using custom Super-Abrasive bonded wheels from Japan, we achieve an unparalleled surface accuracy of 0.03µm for Steel Anvil and Tungsten Carbide rollers, showcasing our commitment to low surface roughness and exceptional precision.
Our tailored approach, rigorous quality control, and cutting-edge technology make us the go-to choice for die regrinding, promising longevity and peak performance for your dies in diverse applications.
- Begin with a thorough assessment of the die cut rollers or flatbed dies.
- Customized Wheel Selection
- Initiate the grinding process using CNC and Hydraulic Grinding machines.
- Maintaining the integrity and performance of the die.
- Rigorous quality control measures at every stage of the grinding process.
- Conclude the process with a final inspection to verify the precision and quality of the regrinded dies.
Second Machining
In our relentless pursuit of precision, we employ advanced vertical machining centres (VMCs) for second machining operations, which are vital in addressing potential dimensional deviations after numerous services.
Specializing in crafting high-accuracy dies, our VMCs enable us to achieve tolerances within the range of ±0.03, ensuring exact dimensions and meeting the stringent standards of diverse industries.
The versatility and efficiency of VMCs allow for intricate adjustments, guaranteeing that each die undergoes a meticulous refinement process.
This commitment to precision, coupled with stringent quality controls, optimizes the longevity and performance of our dies, offering clients reliability and excellence in every product.
- Precision Refinement through Second Machining
- High-Accuracy Die Manufacturing
- Versatility and Efficiency of VMCs
- Tolerance Control
- Optimizing Longevity and Performance
Throughout the second machining operations, our emphasis on quality assurance remains unwavering. Stringent checks and controls are implemented to guarantee that the refined dies not only meet but exceed the targeted dimensions.
Re Sharpening
Our re-sharpening process is meticulous artistry focused on the knife portion, intricately carving to recover the sharpness of the entire tool with originally designed angles and dimensions.
We go beyond mere sharpening; our commitment is to preserve the original design integrity of the tool, ensuring not only restored sharpness but often surpassing the tool’s initial performance.
Quality assurance is paramount at every stage, ensuring the recovered sharpness meets the highest standards. Our re-sharpening service is a testament to precision, where each tool undergoes a rejuvenation process with unparalleled accuracy.
- Focuses on the knife portion with meticulous attention to detail
- Manual Expertise
- Microscopic Visualization
- Preservation of Design Integrity
- Quality Assurance
Using specially graded tools enhances the efficiency and effectiveness of the re-sharpening, allowing us to achieve precision that meets the highest industry standards.
Metalizing
Metalizing, specifically through the application of Hard Chrome plating, is a pivotal technique in revitalizing machinery.
Following continuous use, wear in bearing holding areas on shafts can compromise the fit for bearings.
Our Metalizing process goes beyond surface refurbishment; it represents a comprehensive rejuvenation of critical components.
Through Hard Chrome plating, we deposit a protective layer onto these surfaces, restoring dimensions and enhancing durability.
Precision grinding follows, ensuring the bearing holding areas achieve optimal tolerance levels for a seamless fit with bearings.
This comprehensive approach rejuvenates worn components and extends the machinery's lifespan, fortifying it against future wear and corrosion, ultimately enhancing reliability and performance.
- Precision Restoration
- Extended Machinery Lifespan
- Cost-Effective Refurbishment
- Improved Performance
- Ensuring optimal functionality across diverse applications
Final Testing
Our final testing phase represents a meticulous evaluation of die-cut rollers and anvil rollers, utilizing advanced testing machines equipped with Electronic Variable Frequency Drive (VFD) and Pressure-controlling systems.
This comprehensive approach allows us to precisely vary the speed, identify optimal Pressure, and ensure adherence to customer requirements by using their original product materials.
For anvil rollers, our testing goes beyond speed and pressure assessments, encompassing dimensions checks, surface finish inspections, and run-out tests.
This commitment to thorough evaluations, continuous improvement, and customer-centric testing ensures that our rollers meet and exceed industry standards, delivering reliability and excellence in varied applications.
- Precision Validation
- Customer-Centric Approach
- Comprehensive Testing Machines
- Multi-Faceted Anvil Roller Testing
- Quality Assurance
- Enhanced Manufacturing Standards
- Testimonial
What do our Customers say about us?
Explore experiences shared by our clients. Dive into their feedback for a glimpse into our service quality.
” Our manufacturing improved a lot with these top-quality dies. I highly recommend Sakazaki for its great performance and long-lasting products.”
Industrial Manager
” These dies are durable and efficient, significantly enhancing our manufacturing. Highly recommended for anyone seeking reliable performance and quality products.”
Managing Director
” We’re impressed by the durability and performance of these dies. They’ve significantly enhanced our operations, making them more efficient and reliable .”
Product Manager