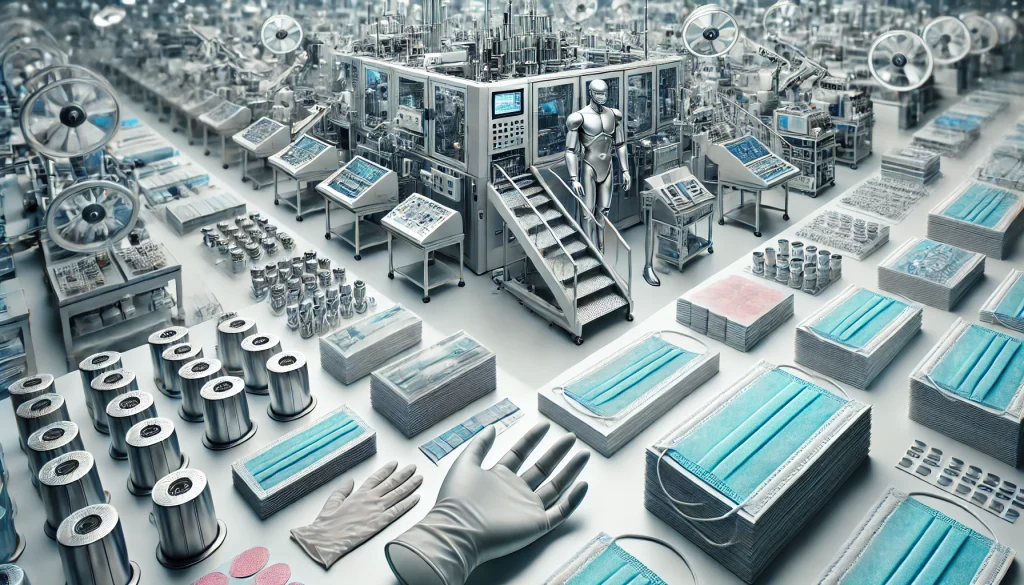
Medical products play a vital role in the healthcare and medical device industries. They are essential tools in manufacturing medical devices, ensuring precision, safety, and quality in the production process. Here, we’ll explore the different types of medical product dies, their applications, and why they are indispensable in medical manufacturing.
What Are Medical Product Dies?
Medical product dies are specialized tools used to shape or cut materials in the production of medical devices. They ensure consistent dimensions and precise cuts and are crucial for maintaining product quality. Manufacturers rely on these dies to meet the rigorous standards of the medical field.
Materials Used in Medical Product Dies
The materials used to manufacture medical product dies are crucial to their functionality. Some common materials include:
Stainless Steel: Known for its strength and durability, stainless steel is often used in dies that require high precision.
Tungsten Carbide: With excellent hardness, tungsten carbide provides extended tool life and precision.
Aluminium: Lightweight and corrosion-resistant, aluminium is used in dies that require less intense strength.
Key Applications of Medical Product Dies
Medical products produce various essential items in the healthcare industry. Here are some common applications:
1. Surgical Instruments
Medical dies are used to shape and cut surgical instruments with accuracy. Stamping dies are valuable in creating scalpel blades, forceps, and scissors that require high precision.
2. Diagnostic Devices
Manufacturers use medical dies to create diagnostic tool components, such as MRI machine parts or blood analyzers. High precision in these parts is crucial for accurate diagnostics.
3. Implantable Devices
Medical devices also help create implantable devices, such as pacemakers and artificial joints. These products must meet strict standards, and using high-quality dies ensures the integrity of each device.
4. Medical Tubing and Catheters
Extrusion dies are essential in producing medical-grade tubing and catheters. To ensure patient safety, these tubes must be uniform in size and free from defects.
Advantages of Using Medical Product Dies
Medical diseases bring several advantages to the production process:
Enhanced Precision: Dies allow for exact cuts and shapes, vital in medical manufacturing.
Consistency in Production: Dies help achieve uniformity across all products, reducing variations.
Increased Efficiency: They speed up production, making the process more cost-effective.
Compliance with Standards: Using dies ensures products meet industry standards, enhancing patient safety.
Maintenance and Care for Medical Product Dies
Proper maintenance of medical dies is essential to prolonging their life and maintaining product quality. Regular cleaning, inspection, and lubrication help prevent wear and tear and ensure reliable performance. Additionally, sharpening cutting edges and re-coating dies can improve longevity.
Conclusion
Medical product dies are indispensable in the manufacturing of medical devices, providing the precision, consistency, and efficiency necessary to meet stringent healthcare standards. From surgical tools to diagnostic equipment, dies ensure that every product meets the required specifications for safety and functionality. Investing in high-quality dies and maintaining them properly is crucial for manufacturers aiming to deliver the best medical devices to the healthcare industry.