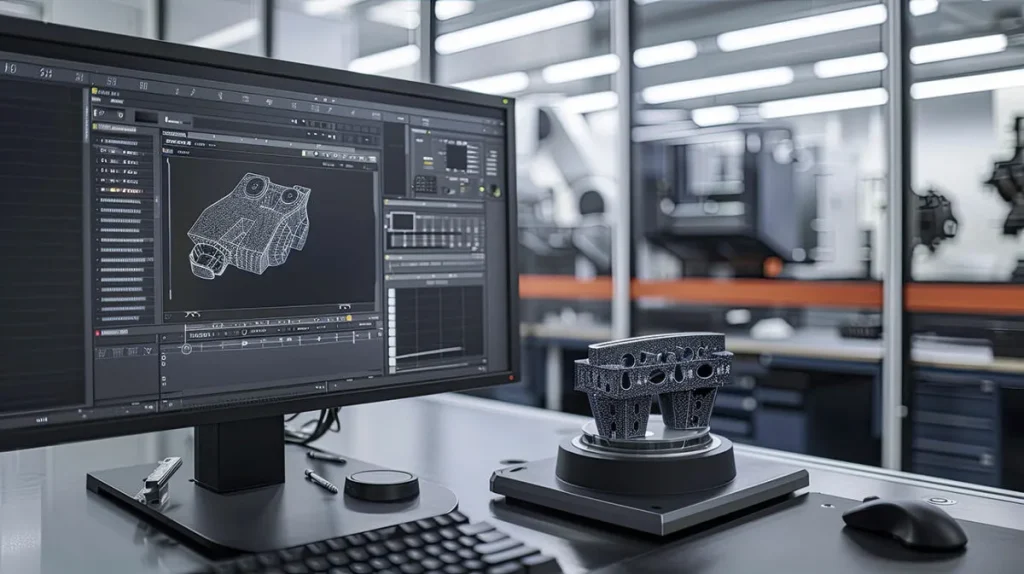
In today’s rapidly advancing manufacturing sector, reverse engineering has emerged as a pivotal technique, especially in industrial die manufacturing. This practice enables companies to enhance precision, optimize production processes, and reduce costs. We uncover how reverse engineering transforms the die manufacturing industry by understanding the intricate interplay between technology and traditional manufacturing techniques.
Reverse Engineering
Reverse engineering involves deconstructing existing products to extract design information and replicate or improve upon them. In industrial die manufacturing, this process allows engineers to capture the geometry of physical objects, analyze their design, and utilize the acquired data for various applications. New-age modern tools like 3D scanners, CAD software, and CNC machines have made this process highly efficient and accurate.
Applications of Reverse Engineering in Die Manufacturing
Recreating Obsolete Parts
One of reverse engineering’s most significant contributions is the ability to reproduce obsolete dies that are no longer manufactured. Industries reliant on older machinery can sustain operations by replicating essential components without relying on original blueprints.
Improving Product Quality
Through reverse engineering, manufacturers can identify flaws in existing designs and implement corrective measures. This leads to dies with enhanced durability, better precision, and improved performance.
Customizing Designs
Reverse engineering empowers manufacturers to create bespoke dies tailored to specific client needs. Customization ensures optimal performance in specialized applications, giving businesses a competitive edge.
Cost and Time Efficiency
Reverse engineering significantly reduces development time and costs by bypassing the traditional trial-and-error design method. The ability to analyze and modify existing designs accelerates the production cycle and minimizes material waste.
Challenges in Reverse Engineering
Despite its advantages, reverse engineering in die manufacturing is not without challenges:
Data Accuracy:
Ensuring the accuracy of scanned data can be difficult, especially for complex or worn-out components.
Intellectual Property Concerns:
Manufacturers must navigate the legal implications of replicating designs, particularly when dealing with patented products.
Technical Expertise:
Skilled professionals must operate advanced equipment and interpret the results effectively.
Future of Reverse Engineering in Die Manufacturing
As technology evolves, reverse engineering is expected to become even more integral to die manufacturing. Innovations in AI, machine learning, and additive manufacturing will likely enhance the efficiency and scope of reverse engineering processes. For instance:
AI-Driven Design Optimization:
Artificial intelligence can analyze scanned data and suggest optimal design improvements autonomously.
Integration with Additive Manufacturing:
Reverse-engineered models can be directly used for 3D printing dies, reducing lead times and costs.
Enhanced Collaboration Tools:
Cloud-based platforms foster collaboration among engineers, enabling seamless sharing and modification of designs across geographies.
Conclusion
Reverse engineering has become a cornerstone of industrial die manufacturing, offering unmatched precision, customization, and efficiency benefits. By leveraging cutting-edge technologies, manufacturers can stay ahead in an increasingly competitive market while meeting the growing demand for high-quality dies. As the field advances, the integration of reverse engineering with emerging technologies promises to reshape the industry further, driving innovation and excellence.