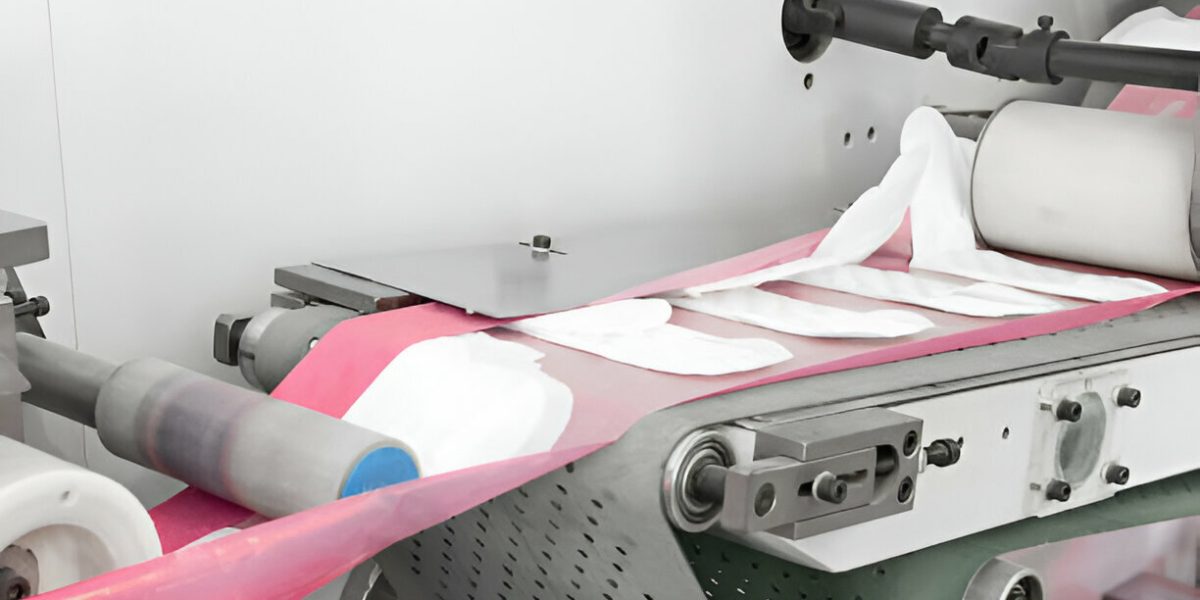
Craftsmanship of Dies in Hygiene Care
Industrial dies play a crucial role in the hygiene care industry, enabling the mass production of essential products such as diapers, sanitary pads, and wet wipes. These intricate tools are at the heart of manufacturing processes, ensuring precision, efficiency, and high quality. This article delves into the craftsmanship behind industrial dies, exploring their design, fabrication, and impact on hygiene care products.
Industrial dies are indispensable in the production of hygiene care products. They are designed to accurately cut, shape, and form materials, ensuring each product meets stringent quality standards. The precision of these dies directly influences the performance and reliability of the final products, which is critical in hygiene care.
Designing Industrial Dies for Hygiene Products
Understanding Material Properties
The design of industrial dies begins with a thorough understanding of the materials used in hygiene products. These materials often include non-woven fabrics, superabsorbent polymers, and various adhesives. Each material has unique properties that must be considered during the die design process to ensure optimal performance.
Precision Engineering
Precision engineering is at the core of die design. Advanced CAD (Computer-Aided Design) software creates detailed models of the dies, allowing engineers to simulate the cutting and forming processes. This ensures that the dies will perform as expected when put into production. The accuracy of these designs is crucial for minimizing waste and maximizing efficiency.
Customization for Specific Products
Different hygiene care products have unique requirements. For instance, the dies used for manufacturing diapers must account for the various layers and components, such as the absorbent core, leak-proof barriers, and fastening systems. Customizing dies to meet these specific needs is essential for consistently producing high-quality products.
Fabrication of Industrial Dies
Selection of Materials
Fabricating industrial dies involves selecting the right materials to ensure durability and longevity. High-grade tool steels are commonly used due to their hardness and resistance to wear. These materials can withstand the rigours of high-volume production, maintaining their precision over extended periods.
Advanced Manufacturing Techniques
Modern manufacturing techniques, such as CNC (Computer Numerical Control) machining, wire EDM (Electrical Discharge Machining), and laser cutting, are employed to fabricate industrial dies. These techniques offer high precision and repeatability, ensuring that each die meets the exact specifications of the design.
Heat Treatment Processes
Heat treatment is a critical step in the fabrication of industrial dies. This process involves heating and cooling the die materials to enhance their hardness and durability. Proper heat treatment ensures that the dies can maintain their sharpness and resist wear, even under the demanding conditions of mass production.
Ensuring Quality and Consistency
Rigorous Testing and Inspection
Industrial dies undergo rigorous testing and inspection to ensure the highest quality and consistency. This includes dimensional checks, material hardness tests, and performance evaluations. Any deviations from the specifications are corrected to maintain the integrity of the dies.
Maintenance and Refurbishment
Regular maintenance and refurbishment are essential to extend the lifespan of industrial dies. This involves sharpening, polishing, and repairing any worn or damaged components. A well-maintained die can significantly reduce downtime and production costs, ensuring a steady supply of high-quality hygiene products.
Impact on Hygiene Care Products
Enhancing Product Quality
The craftsmanship of industrial dies directly impacts the quality of hygiene care products. Precision-engineered dies cut and form each product to exact specifications, ensuring consistent performance. This is particularly important for products such as diapers and sanitary pads, where any deviation can affect their effectiveness and user comfort.
Improving Production Efficiency
Efficient dies contribute to higher production rates and lower costs. By minimizing material waste and reducing the need for rework, these dies enable manufacturers to produce large quantities of hygiene products quickly and cost-effectively. This efficiency is crucial for meeting the growing global demand for hygiene care products.
Driving Innovation
The continuous improvement of industrial dies fosters innovation in the hygiene care industry. Advanced die designs enable the development of new products with enhanced features, such as improved absorbency, better fit, and increased comfort. This innovation drives market growth and provides consumers with superior hygiene solutions.
Conclusion
The craftsmanship of industrial dies is a cornerstone of the hygiene care industry. From the initial design phase to fabrication and maintenance, every step is meticulously executed to ensure precision and quality. These dies enhance the performance of hygiene products and drive efficiency and innovation in manufacturing processes. As the demand for hygiene care products continues to rise, industrial dies will remain vital in delivering high-quality, reliable solutions.