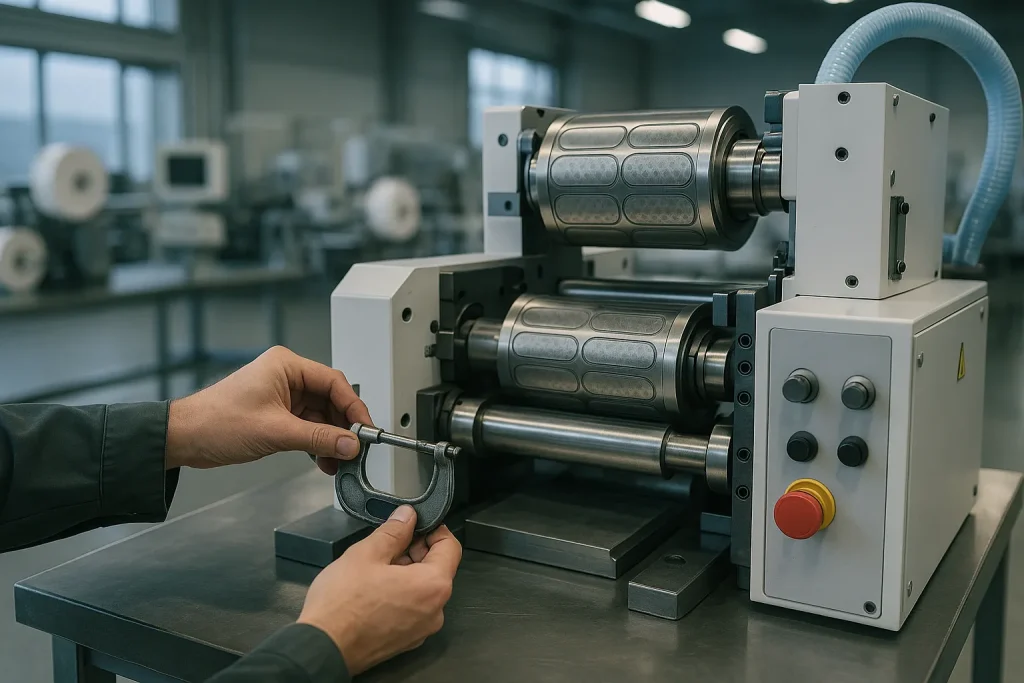
In high-precision industries such as packaging, medical device manufacturing, and electronics, even the smallest variation in cut quality can result in significant downtime, material waste, or product rejection. Rotary die units—critical tools in roll-to-roll converting—are expected to deliver thousands of accurate cuts over extended production cycles. But over time, even the most robust rotary dies begin to show signs of wear and inefficiency.
If your production line is slowing down or quality is slipping, it might be time to ask: Is your rotary die unit underperforming? And more importantly—is it time to rebuild rather than replace?
What Causes Rotary Die Underperformance?
Several factors can reduce rotary die performance, including:
- Blade wear and dull edges
- Thermal expansion from high-speed operations
- Material buildup or residue contamination
- Misalignment due to worn bearings or pressure issues
- Surface damage from abrasive or layered materials
These issues lead to symptoms like uneven cutting, burrs, edge fraying, material sticking, or off-registration—signs that your die may no longer meet tolerance specifications.
Rebuild vs. Replace: Which Makes Sense?
Purchasing a brand-new rotary die unit isn’t always the best solution—especially when time, cost, and existing machinery compatibility are critical. Rebuilding a die unit can be faster and significantly more economical, restoring your tool’s original functionality without the wait of weeks for a custom replacement.
That’s where Sakazaki’s rotary die rebuilding services make a decisive difference.
How Sakazaki Restores Die Performance
Sakazaki specializes in die rebuilding and refurbishing underperforming rotary die units to meet or exceed OEM performance standards. Here’s how:
Comprehensive Unit Inspection
Each rotary die is disassembled and inspected under high-magnification optics to identify microfractures, wear patterns, or misalignments that may not be visible during standard maintenance.
Precision Grinding and Recutting
Sakazaki uses state-of-the-art grinding machines and recutting processes to restore razor-sharp precision to die edges while maintaining the original geometry and cutting angles.
Component Rebuilding and Replacement
Damaged bearings, misaligned shafts, and worn bushings are replaced with high-quality components to ensure flawless rotary motion and consistent pressure across every cut.
Cleaning and Anti-Adhesive Coating
Built-up residues and adhesives are cleaned with precision, and optional coatings, such as non-stick or anti-static finishes, can be applied to reduce future buildup.
Rebalancing and Final Testing
After the rebuild, all rotary units are dynamically rebalanced and tested on simulated production lines to ensure vibration-free, high-speed operation.
When Should You Rebuild? Look for These Signs
- You’ve noticed material jamming or excessive waste.
- Die edges are visibly worn or chipped.
- There is a drop in line speed or more frequent stoppages.
- Quality audits show inconsistent depth or off-centre cuts.
- You’re facing long lead times for new dies.
If any of these apply, it’s time to consider Sakazaki’s rebuild program—a cost-effective way to restore full performance.
Case Insight: Medical Patch Manufacturer
A major medical device company producing adhesive wound care patches was struggling with dimensional inconsistencies and adhesive buildup. Rather than sourcing a new die, they approached Sakazaki for a rebuild. Within days, the refurbished die delivered better-than-new performance, cutting costs and eliminating production delays.
Conclusion: Don’t Replace It—Rebuild It
Underperforming rotary dies are more than a nuisance—they’re a bottleneck to productivity. Rebuilding your existing die unit can bring it back to life more quickly and affordably than replacement. With Sakazaki’s advanced refurbishment expertise, you get reliability, precision, and support you can trust—backed by decades of die-cutting innovation.
Do you think your rotary die is slowing you down? Contact Sakazaki today to explore our precision rebuild services and get your production back on track.