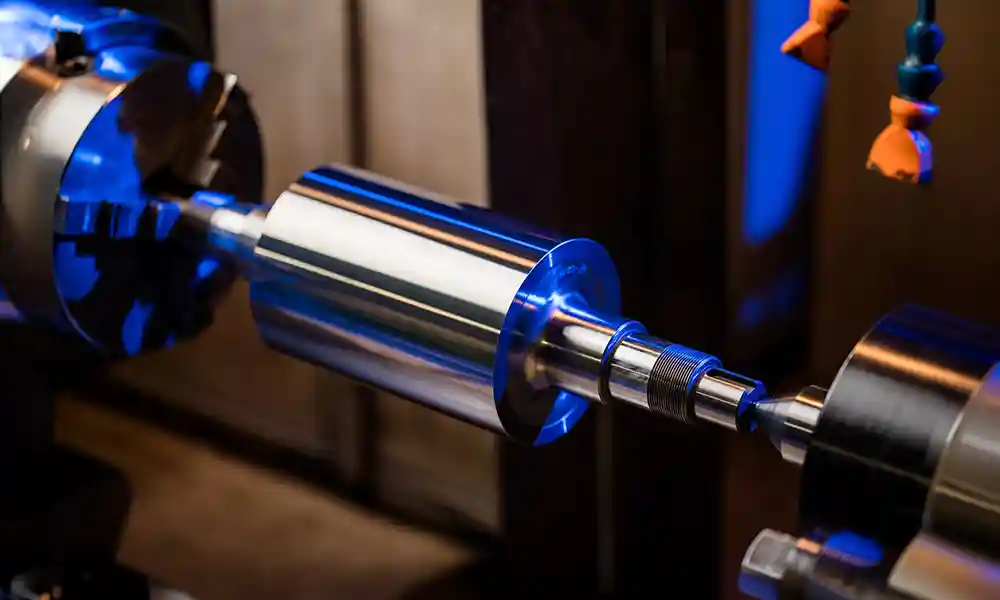
Introduction
In manufacturing, dies play a critical role in shaping and cutting materials with precision. Over time, these dies undergo wear and tear, leading to inefficiencies and product defects. Instead of replacing worn-out dies, manufacturers can opt for die rebuilding—a cost-effective and sustainable solution that restores the die to optimal working conditions. This blog delves into the importance of die rebuilding, its benefits, and how businesses can implement best practices to maximize its effectiveness.
What is Die Rebuilding?
Die rebuilding is the process of restoring worn or damaged dies to their original or enhanced condition. It involves several steps: assessment, disassembly, repair, reassembly, and testing. By refurbishing existing dies, manufacturers can avoid the high costs of purchasing new dies while maintaining production efficiency.
Benefits of Die Rebuilding
Cost SavingsPurchasing new dies can be expensive. Rebuilding extends the life of existing dies, reducing capital expenditure while maintaining performance.
Extended Lifespan:
Regular maintenance and rebuilding prevent premature die failure, allowing manufacturers to use the same die for an extended period.
Improved Product Quality:
Rebuilt dies function as efficiently as new ones, ensuring that products meet the required quality standards.
Reduced Downtime:
A well-maintained die minimizes unexpected breakdowns, keeping production lines running smoothly.
Sustainability:
Recycling and refurbishing dies contribute to eco-friendly manufacturing by reducing material waste.
Key Steps in Die Rebuilding
Inspection and Damage Assessment:
The first step in die rebuilding is a thorough inspection to identify wear, cracks, or damage. Advanced diagnostic tools help detect underlying issues.
Disassembly and Cleaning:
The die is carefully dismantled, and all components are cleaned to remove debris, grease, and residues.
Repair and Machining:
Worn-out or damaged sections are repaired using precision machining, welding, or replacement of specific parts.
Reassembly and Alignment:
After repairs, the die is reassembled with precise alignment to ensure proper functioning.
Testing and Quality Control:
The rebuilt die undergoes rigorous testing to verify its performance before being returned to production.
Best Practices for Die Maintenance
Regular Inspections: Conduct routine checks to detect early wear signs and promptly address issues.
Proper Lubrication: Use high-quality lubricants to minimize friction and extend the die’s lifespan.
Operator Training: Ensure staff are trained in proper die handling and maintenance procedures.
Data Tracking: Maintain records of die performance, repairs, and maintenance schedules for continuous improvement.
Conclusion
Die rebuilding is an essential practice in manufacturing that helps companies save costs, improve efficiency, and contribute to sustainable production. By adopting a proactive maintenance strategy and following best practices, manufacturers can extend the lifespan of their dies, reduce downtime, and maintain high-quality output. Investing in die rebuilding ensures a reliable and cost-effective manufacturing process that benefits businesses and the environment.